Inventory Management
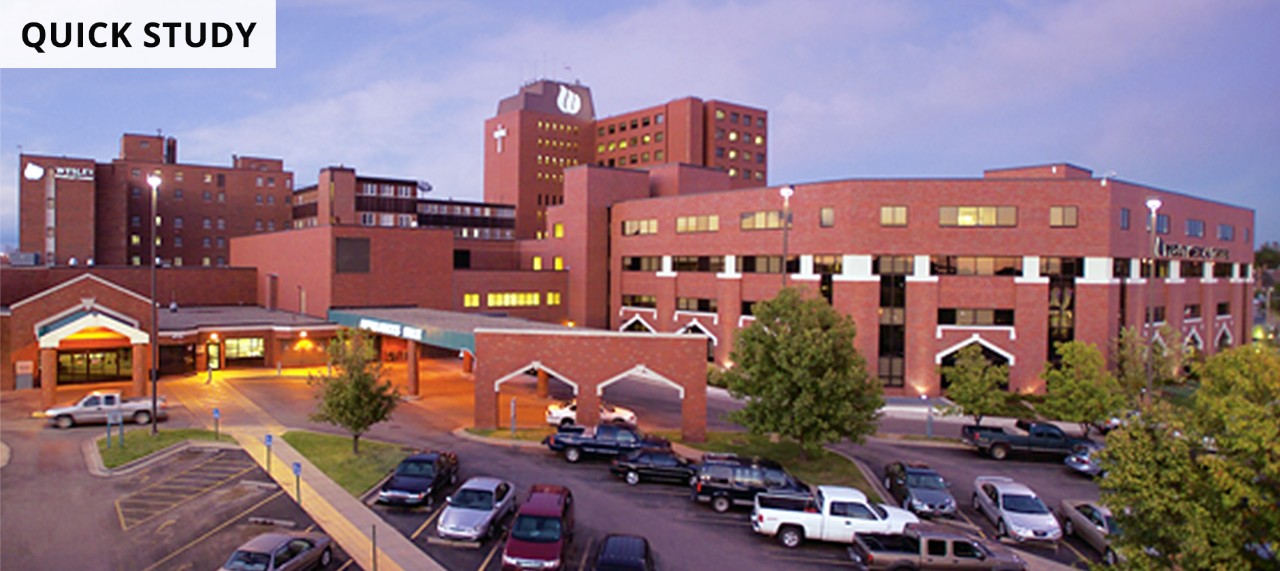
How Wesley Medical Center minimized expired products to get more than "bottom line" results
The challenge
The Endoscopy department Wesley Medical Center, a 700-bed hospital in Wichita, Kansas, performs 400 to 500 procedures a month, mainly outpatient. The facility did not have the time, bandwidth or budget to allow for expired endoscopy supplies, or to carry nearly $200,000 worth of endoscopy inventory at any given time to avoid supply shortages.
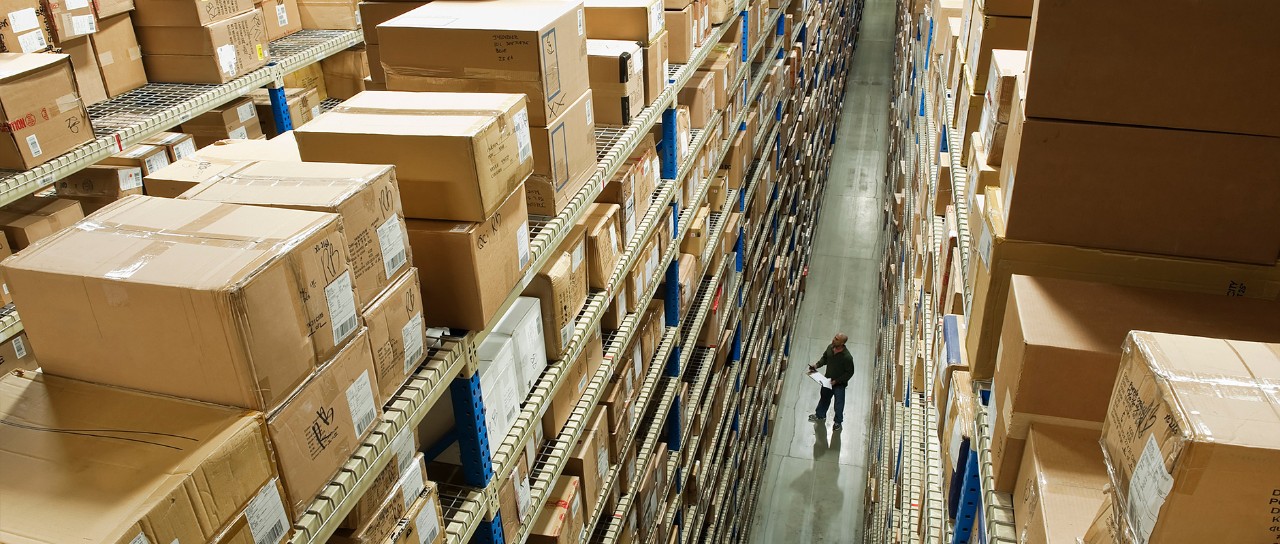
The solution
Working with Boston Scientific’s ADVANTICS™ Innovative Healthcare Solutions, the facility set out improve its ordering processes to improve inventory management and reduce expired products.
Boston Scientific account representative Jonathan Gutierrez collaborated with Assistant Nurse Manager Lindy Clingan. In talking to the staff, they heard complaints about expired inventory ranging from inexpensive supplies up to higher-cost medical devices. They were overstocked on some items, running out of others, and making do with substitute items at times.
As a first step, Boston Scientific worked with a third-party to conduct an initial count of Boston Scientific endoscopy products. From the inventory count, order history data and knowing what items frequently run low, Boston Scientific recommended “par levels” for each category of Boston Scientific products ordered. The par levels were then used to determine order amounts for each supply based on procedure mix estimates. Going forward, weekly counts are necessary to determine order quantities and track expirations.
Clingan went on to implement additional streamlining of ordering processes to the point where Wesley has now halved its number of orders per week. She also moved the supply chain workflow process from paper to digital and consolidated the department’s ordering processes and inventory tracking. By doing so, the department decreased the total number of orders and reduced inventory on hand from roughly $180,000 to $120,000.
“You don’t realize, until you don’t have to do inventory counts anymore, how much time it takes,” says Clingan, who now relies on Boston Scientific to do the counting of its products. “With that type of support, department managers should be able to implement this type of workflow process in any facility.”
Replicating inventory processes for improvements in your department
- Get your vendors involved in counting inventory and checking for expired items, which reduces staff overhead and frees up time for patient care.
- Show the hospitals accrediting organization The Joint Commission - whose surveys determine whether or not you can take Medicare patients - what you're doing. In the midst of the endoscopy inventory management makeover, Wesley underwent its accreditation survey. Clingan outlined to surveyors what she was doing to improve her department, which helped earn high marks.
- Set a goal for improvement - so you know what success looks like.
- Divide and conquer unwieldy inventory and ordering processes by assigning different categories of supplies to different staffers within the department, and making them accountable for for items in stock. In Clingan's department, that means one nurse handles pulmonary supplies, another takes care of general supplies, another endoscopic retrograde cholangiopancreatography (ERCP), etc.
Insights
According to Clingan, it’s not just the hospital’s bottom line that benefits from projects like these. Having the right supplies at the right time in the workflow directly impacts patient care and satisfaction. When substitute supplies aren’t being used or procedures don’t have to be rescheduled due to lack of on-hand supplies, patients get the best experience possible. It also helps increase staff efficiency and satisfaction, because they’re not hunting through expired product to find one that’s usable for the next patient.
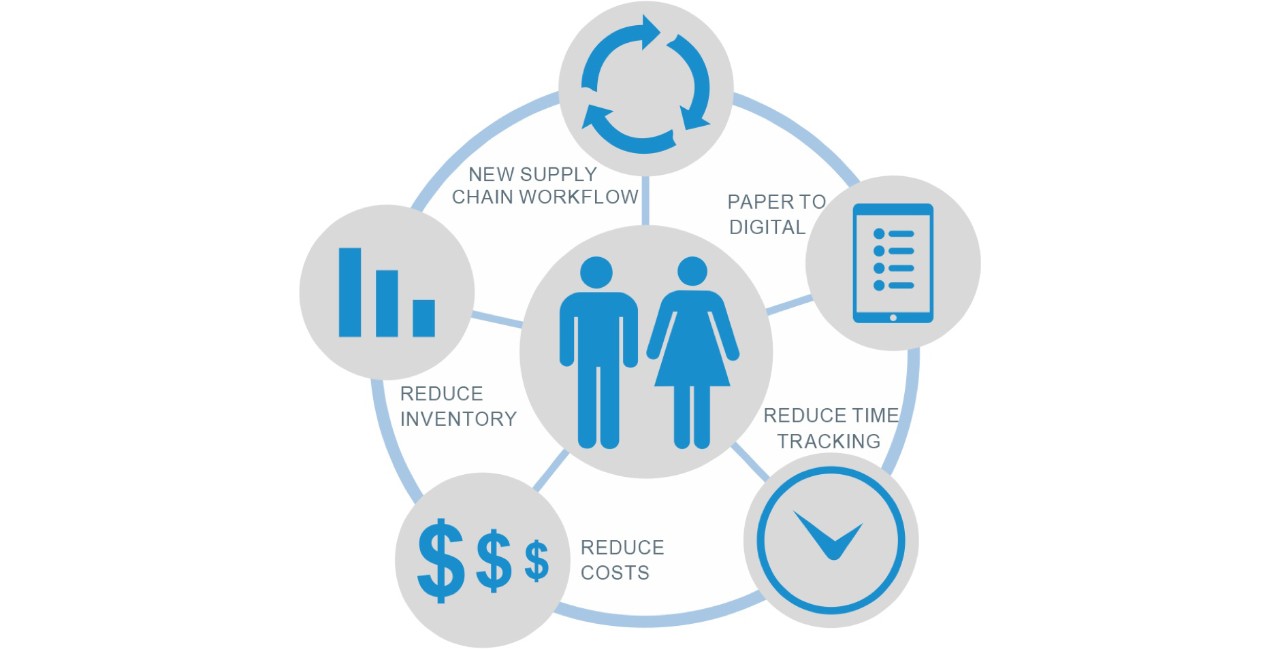
Insights
According to Clingan, it's not just the hospital's bottom line that benefits from projects like these. Having the right supplies at the right time in the workflow directly impacts patient care and satisfaction. When substitute supplies aren't being used or procedures don't have to be rescheduled due to lack of on-hand supplies, patients get the best experience possible. It also helps increase staff efficiency and satisfaction, because they're not hunting through expired product to find one that's usable for the next patient.
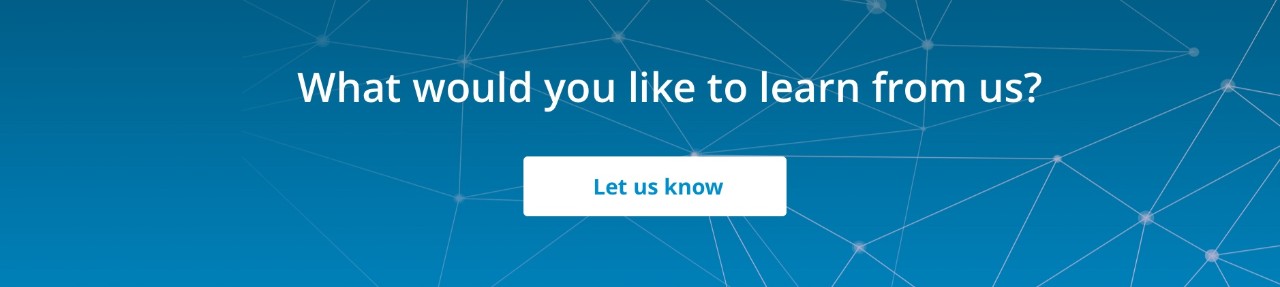